The Ultimate Guide to Automotive Racks Design: Space-Saving, Heavy Duty for Efficient Packaging
- Bk Engineering
- Jan 31, 2024
- 10 min read
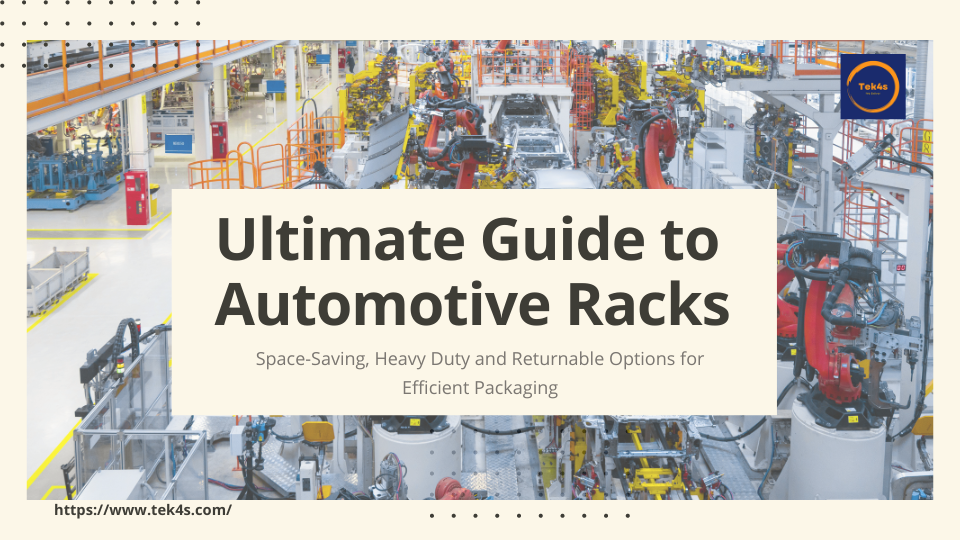
Introduction to Automotive Rack Design
Automotive rack design plays a critical role in protecting parts during packaging, storage, and shipping. Custom-designed racks provide significant advantages over universal off-the-shelf options for companies that manufacture, distribute, or sell automotive parts.
Racks create structure within packaging and shipping containers to securely hold and separate components. This prevents damage from vibration, shocks, moisture, dust, and other hazards encountered in transit and storage. Well-designed racks also optimize the available space, allowing more parts to be loaded in a standardized crate or trailer.
The unique nature of automotive parts requires rack designs tailored to each component's shape, weight, sensitivity, and packaging quantity. Custom racks properly secure the part and maximize density. They distribute weight evenly within the container and immobilize parts to prevent abrasion. Racks can be designed to be collapsible, nestable, stackable, and reusable - optimizing transport and storage between uses.
Suppliers of automotive tooling also utilize heavy-duty racks for safe handling and corrosion prevention. Custom racks can incorporate drawers, doors, and shelves when needed for access and organization. Robust steel construction ensures these critical molds and dies avoid damage.
In summary, automotive racks provide specialized protection, density, accessibility, and reusability - all vital for efficient packaging and shipping. Custom designing racks for each part saves costs over one-size-fits-all racks and reduces product damage substantially. Continued innovation and optimization of automotive rack designs will drive progress in global automotive supply chains.
Key Considerations for Automotive Rack Design
Effective rack design for automotive parts requires balancing several key factors. The primary considerations are:
Protecting Parts from Damage
Protecting fragile and expensive automotive components from damage is the top priority. Racks should securely hold parts to prevent movement and absorb shocks during transit. Custom racks shaped to each part ensure maximum protection. Extra cushioning or secure tiedowns can be added. The rack strength and durability should match part weight.
Load Capacity
The rack must safely handle the weight of the automotive parts being stored or transported. Load capacity ranges from 500 lbs for small racks up to 10,000+ lbs for industrial racks. Heavier parts require more structurally reinforced racks. Consider both static and dynamic load capacity.
Material Selection
Steel is the most common rack material due to its strength. The gauge (thickness) should suit the load. Aluminum is lighter but less strong. Plastics can provide cushioning. Solid decking provides maximum support. Consider corrosion resistance needed.
Collapsibility and Nesting
Collapsible and nestable racks optimize space efficiency. Empty racks collapse down when not in use for compact storage. Nesting allows racks to stack tightly together to maximize inventory density.
Mobility
Stationary racks limit movement flexibility. Mobile racks on casters can be easily moved around a facility. Forklift movable racks facilitate loading and unloading. Mobility helps improve warehouse efficiency.
Careful consideration of these key factors allows designing optimized racks to safely organize, store, and transport automotive parts to reduce damage while improving space and material handling efficiency. Custom designs match the specific components and operational needs.
Common Rack Types for Automotive Parts
Automotive parts come in all shapes and sizes, from small nuts and bolts to large body panels and engines. Rack design needs to accommodate the wide variety of components efficiently and safely. Here are some of the most common types of racks used for automotive parts:
Component Racks
Component racks hold smaller parts like hoses, wiring harnesses, radiators, headlights, and more. They often feature dividers and bins to organize parts and prevent tangling. Stackable component racks maximize density, while roll out racks provide easy access. Structural component racks securely store heavier items.
Body Panel Racks
Body panel racks transport and store larger exterior body components like doors, hoods, roof panels, fenders and bumpers. They feature protective pads to prevent scratches and dents. Telescoping arms allow panels to be loaded and unloaded easily. Some body panel racks are collapsible for transport and storage efficiency.
Engine/Transmission Racks
Engine and transmission racks securely cradle these heavy and expensive powertrain components. They are constructed from structural steel or heavy duty pallet racking. Many include ratchet tie downs, protective padding, and custom crating. Forklift skids make it easy to transport loaded engine racks.
Tire Racks
There are many styles of racks designed to hold passenger vehicle and truck tires. These include vertical stack racks, boltless racks, teardrop racks and carousels. Most tire racks have a slotted design to prevent rolling and level shelving for stability. Mobile tire racks can improve warehouse efficiency.
Sheet Metal Racks
Sheet metal storage racks provide a safer and more organized way to store metal sheets versus wood pallets. They are available in stationary or mobile designs. Features like roll out shelves make loading and unloading easier. Sheet racks have high weight capacities up to 5,000 pounds.
The variety of rack types allows automotive facilities to customize storage and transportation solutions. Utilizing the right racks for each part type optimizes space usage, accessibility and safety.
Optimizing Space with Rack Design
One of the biggest considerations for rack design in automobile packaging is maximizing storage space. Automotive parts warehouses, distribution centers, and manufacturing facilities all have limited floor space that needs to be optimized. Rack systems can improve space utilization through vertical storage, compact footprints, stackable and nestable designs, and racks tailored to specific facilities.
Using vertical space efficiently is key. Multiple levels of racks and shelves allow you to store more parts per square foot. High density vertical racks have a smaller footprint compared to single level racks and shelving. Mezzanines and multi-tier systems also help maximize cubic volume.
Stackable rack designs allow multiple racks to be stacked when not in use, collapsing vertical space. Tires, body panels, pallets and other racks can compact for storage but expand when loaded. Nestable racks fit tightly together when empty. This allows empty racks to take up less warehouse space and be staged out of the way.
Automotive racks should be designed based on the size and shape constraints of the facility. What types of storage racks fit in the aisle space? How much clearance is there for fork lifts and material handling? Custom racks sized specifically for the warehouse or manufacturing floor plan save valuable real estate.
Optimizing space utilization is crucial given the high value and volume of automotive inventory. Proper rack and storage design tailored to the facility results in major space savings.
Heavy Duty Racks for Automotive Tools
Automotive manufacturing facilities require rugged rack systems to safely store heavy machinery, tools, dies, and molds. These racks need to withstand constant use in demanding industrial environments. Structural steel I-beam construction provides the strength and rigidity required for heavy automotive tooling racks.
Tool and Die Racks
Tool and die storage racks utilize a reinforced I-beam frame with heavy gauge shelving. These racks maximize storage density while providing the structural integrity to handle high tooling weights. Common capacities range from 5,000 lbs to 10,000 lbs per shelf level. Features like seismic braces, pull-out shelves, and modular components enable racks to be customized for specific tools.
Racks for Molds and Fixtures
Steel pallet racks and cantilever racks offer robust storage solutions for heavy automotive molds and fixtures. They allow easy access from forklifts while keeping molds organized and secure. Movable arms on cantilever racks let operators quickly load and unload hefty automotive components. Wide spanning I-beam pallet racks can accommodate varying mold sizes. Racks are often designed to interlock for space efficiency.
I-beam construction and sturdy decking provide the strength to securely store these critical automotive assets. Proper rack systems with high load capacities prevent damage and distortion that could occur to molds and fixtures. This helps maintain quality and extend tooling service life. Heavy duty racks also improve shop floor safety by stabilizing heavy machinery.
Easy Access with Roll Out Racks
Roll out racks provide easy access to stored automotive parts with retractable cantilevered arms or shelves. This allows workers to bring the parts to them, reducing walking, bending, and potential lifting injuries.
Roll out racks come in stationary and mobile configurations. Stationary roll outs are installed along assembly lines or in parts storage areas. They allow efficient access to work in progress parts without having to leave the line.
Mobile roll out racks can be wheeled to the point of use and staged there. Some models have removable cantilevered arms or shelves that can be quickly detached and brought directly to the assembly point.
The extendable cantilevered arms on roll out racks allow shelves or parts to be presented for easy loading and unloading. This is an ergonomic alternative to reaching deep inside traditional shelving units.
Many roll out models have weight capacities ranging from 500 to 5000 pounds per cantilevered arm or shelf. This allows them to handle everything from small components to heavy automotive body panels.
Roll out racks with retractable shelves bring stored items to the worker at an ergonomic work height. This eliminates excessive bending, lifting, lowering, and twisting movements that can lead to injury over time.
Automotive suppliers often use roll out racks for work in progress (WIP) storage at assembly stations. Parts can be stored right at the point of use, enhancing workflow. The racks provide fast access to parts without wasting time walking back and forth to a storage area.
Overall, roll out racks boost productivity and safety through easy access to parts. Their retractable design presents items at an ergonomic position for workers. This leads to a more efficient process that is safer on the body over time.
Returnable Shipping Racks Maximize Reusability
Returnable shipping racks provide an efficient and environmentally friendly way to protect automotive parts during shipping and transport. These custom-designed racks are built to securely hold specific components, preventing damage over many trips between suppliers, manufacturers, and other facilities. Reusing shipping racks has financial and operational benefits compared to disposable, one-way packaging methods:
Custom Fit for Each Part
Racks are custom-engineered based on part shape, weight, size, and quantity
Cradles and dunnage secure the component in place
No excess movement during handling and transport
Avoids using excess packaging materials
Durable for Multiple Shipments
Heavy duty steel construction withstands vibration, shock, and load shifts
Powder coated paint protects from moisture and corrosion
Designed to be collapsible, stackable, and easy to store when not in use
Reused for the life of program production
Cost Savings Over Time
Returnable racks average 5-15 uses before refurbishing
One-time investment over years of service
Reduces material, labor, and disposal costs of one-way packaging
Lowers per unit transport cost as reuse increases
Streamlined Process
Eliminates steps of removing and replacing packaging at each stop
Standardized containers speed loading/unloading
Trackable for logistics monitoring and maintenance planning
Simple to clean and inspect for defects between uses
Returnable shipping racks enable automotive OEMs and suppliers to protect parts through the entire supply chain while minimizing costs and materials. Custom engineered to each component, these reusable racks provide an efficient and sustainable packaging solution.
Material Handling Considerations
When designing racks for automotive parts and packaging, it's crucial to consider material handling compatibility. The racks need to integrate with other systems and equipment in your warehouse or facility.
Compatibility with Conveyors, AGVs, and Forklifts
Many facilities use conveyor systems, automated guided vehicles (AGVs) and forklifts to transport racks. The rack design should allow for easy loading and unloading from these material handling systems. Consider the size and clearance required to fit on conveyors. Account for turn radii if using AGVs to avoid collisions. And ensure racks can be safely lifted and accessed by forklifts.
Racking Systems
Look at how the racks will be stored and accessed in inventory racking systems. Measure the dimensions and weight capacity of shelving and space between uprights. This ensures the racks are sized appropriately and structurally sound when loaded on racks. Consider if a flow rack or push-back rack system is preferred to access the racks.
Transporting Loaded Racks
Design the racks so they can be safely and securely transported when loaded with automotive parts. Include tie-down points, consider the overall size and center of gravity, and choose durable casters that can handle the load if designing mobile racks. Proper transport of loaded racks prevents damage, part loss, and safety hazards.
Thinking through these key material handling factors when designing automotive racks ensures they integrate smoothly in your facility. It allows efficient movement of racks between workstations, conveyors, racking, and loading docks. The optimal rack design accommodates all your material handling processes.
Rack Design for Safety
Safety should always be a top priority when designing racks for automotive packaging and storage. There are several key considerations:
Load Limits
Racks should be clearly labeled with maximum load limits per level or section
Load limits help prevent overloading and possible collapse or damage
Consider both static and dynamic loads during transportation
Attachment Points
Properly designed attachment points are critical
Forklift tubes, pockets, and entryways should be reinforced
Attachment points distribute load forces evenly
Forklift Pockets
Entryways for forklift tines should allow easy access
Ample clearance avoids accidental impact during loading
Forklift pockets may have removable gates for security when not in use
Labels and Instructions
Warning labels, load limits, diagrams, and instructions should be clearly displayed
Diagrams can show proper lifting points, storage configuration, etc.
Instructions should cover assembly, stacking, transport, and maintenance
Following rack safety best practices protects inventory, workers, and equipment. Consulting with experienced engineering teams ensures racks meet all application requirements. Safety and performance testing is also recommended.
The Future of Automotive Rack Design
Automotive rack design continues to evolve just like the vehicles and parts they transport and store. Here are some of the key trends and innovations shaping the future of the industry:
Lighter Weight Materials - One major shift is using lighter weight yet durable materials in rack construction. Traditional steel and metal alloys are being replaced by composites, carbon fiber, plastics, and aluminum in certain applications. This allows for increased fuel efficiency and handling when transporting racks. It also reduces strain on workers handling the racks repeatedly. Lighter racks can maximize the cargo weight capacity of vehicles as well.
RFID Tracking - RFID chips and sensors are being integrated into rack systems to enable real-time tracking and inventory management. Racks can transmit location data wirelessly to provide insights into stock levels, throughput, and bottlenecks. This automation allows warehouses to optimize rack usage and layout. RFID also facilitates quick product recalls if needed.
Automation Integration - Racks are being designed for seamless integration with robotic pickers, automated storage and retrieval systems, conveyors, guided vehicles, and other automated warehouse equipment. Standardized rack sizes and connections allow robots to interface efficiently. Racks can also charge automated guided vehicles on the go.
Ergonomic Designs - New racks are incorporating ergonomic features to reduce physical strain on workers. This includes optimized working heights, lift assists, wheels/casters for mobility, and angled shelves to avoid excessive reaching and bending during loading/unloading. Simple aids like shelf labels, location markers, and color coding further ease identifying and accessing contents.
Modular Flexibility - Modular and reconfigurable rack designs allow organizations to quickly adapt their storage layouts to changing needs. Shelves, arms, dividers, and other components can be added, removed, or adjusted with minimal downtime. This agility is essential for the fast-paced automotive sector.
As rack technology progresses in step with wider supply chain innovations, organizations can look forward to even more durable, safe, and efficient solutions for their automotive inventory management needs.
コメント